Ashuganj’s Century-Old Rice Market Home / BOC Ghat sits about...
Read More400 Years of Dhakai Jamdani: Mughal Era to Modern Bangladesh
Jamdani is a traditional Bengali handwoven textile, known for its intricate patterns and rich heritage, dating back over 400 years. Originating from the Mughal era, it remains a symbol of craftsmanship and cultural pride in modern Bangladesh.
400 Years of Dhakai Jamdani: Mughal Era to Modern Bangladesh
In ancient times, fine muslin fabric was woven using cotton yarn through the traditional handloom process. The intricately designed or patterned fabric woven on muslin was known as Jamdani.
Although Jamdani is commonly associated with sarees, in reality, it includes a wide range of traditional items such as scarves, kurtas, turbans, skirts, handkerchiefs, curtains, and tablecloths—all adorned with intricate designs.
Under the scorching heat, artisans operate the loom with bare bodies. With their skilled hands, they weave various patterns into the Jamdani fabric using fine threads.
This labor-intensive work continues from morning till night. In Narayanganj, this vibrant loom-based craftsmanship is a familiar sight in the homes of weavers.
History and making of Jamdani saree
The art of dyeing thread using special techniques has been practiced for nearly 400 years. This tradition dates back to the Mughal era and is a cultural heritage of Narayanganj.
During the Mughal period, the muslin woven by Bengali weavers captivated the hearts of people around the world.
Although muslin was produced in various parts of the Indian subcontinent, the major production centers of undivided Bengal were Dhaka, Murshidabad, and Shantipur.
Among them, the muslin produced in Dhaka and its surrounding areas was considered the finest in terms of both quality and design.
When Dhaka became the capital of undivided Bengal in 1610, under the patronage of Mughal Emperor Jahangir, the weavers of that time successfully established the brand of Dhakai Muslin.
Based on the variation in thread count, 28 types of muslin fabric used to be woven. Muslin fabric that featured intricate embroidery or design on a plain base was known as Jamdani.
Among those 28 types, Jamdani is the only one that has survived and continues to exist in Bangladesh today.
Rupganj in Narayanganj was one of the many weaving hubs in the Dhaka region of undivided Bengal, and it was especially popular for producing Jamdani.
The descendants of those weavers in Rupganj are still carrying forward the legacy of Dhakai Muslin, now known as Dhakai Jamdani.
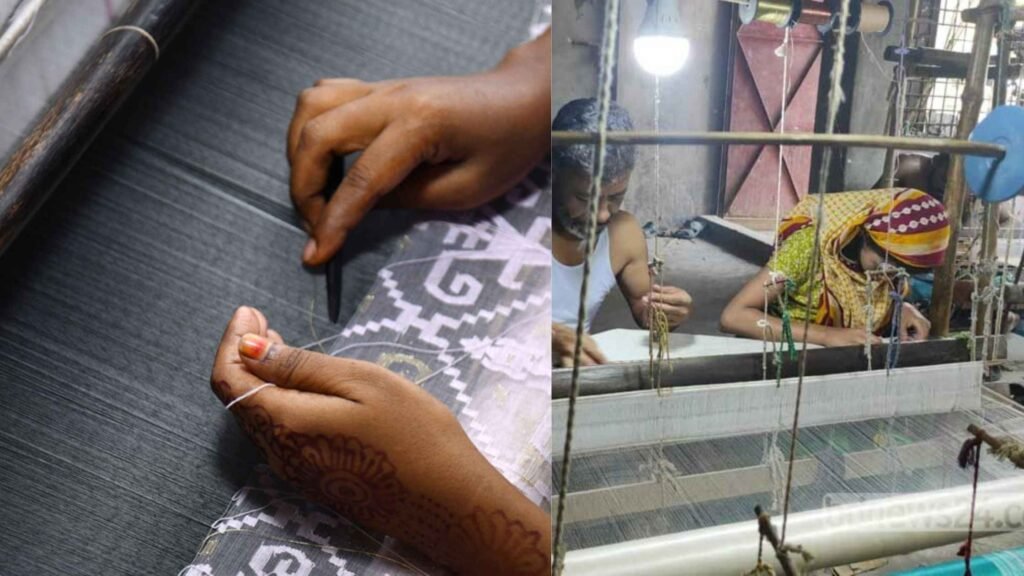
Traditional Art of Weaving Jamdani
The weavers of Rupganj bring their Jamdani weaving threads from Narayanganj. Most weavers buy plain white thread and dye it themselves at home to create colorful yarns.
Some, however, purchase pre-colored threads based on their needs.
Threads are sold in belts, and the price of each belt varies according to the thread’s count. Since the fine threads are very delicate and can tear with the slightest mishandling, Jamdani weavers do not use motorized looms.
Instead, they continue the tradition of weaving with hand-operated spinning wheels.
In each weaving house, two artisans work together, sitting side by side. They must weave in perfect harmony to maintain the parallel alignment of the threads, which is crucial for crafting the saree and its intricate patterns.
This unique weaving technique of Jamdani was recognized in 2013 by UNESCO as a World Intangible Cultural Heritage of Humanity.
Since Jamdani work is entirely handmade, it requires a rare combination of patience, focus, and skill.
Payment System of Jamdani Technician
This labor-intensive craft is something the younger generation is no longer interested in learning. As a result, the weavers fear that, like Muslin, the artisans of Jamdani may also disappear in the near future.
Despite numerous challenges, the weavers of Jamdani continue to carry forward this UNESCO-recognized cultural heritage of Bangladesh with endless patience, inherited knowledge, skill, and love for the craft.
The artisans are paid based on contracts per saree, with wages varying depending on the complexity of the design. Each weaving house typically has 10 to 20 looms.
These weaving houses are built with a special design, using a combination of bamboo, tin, wood, and concrete, ensuring proper airflow.
The quality of Jamdani’s delicate threads is affected by the humidity in the air, which is why the weaving houses are designed to be open and airy.
Glorious Legacy of Jamdani Mentioned by Ibn Battuta
The famous 14th-century traveler Ibn Battuta mentioned the exquisite Jamdani of Sonargaon in his travel writings, highlighting its unmatched designs.
Though many of those golden-age patterns have disappeared over time, the weavers of Rupganj, Sonargaon, and Siddhirganj in Narayanganj still preserve the quality and heritage of those legendary designs to this day.
Where to buy authentic Jamdani saree in Bangladesh ?
Instead of high-end showrooms in big cities, Jamdani sarees can be bought at a much lower price directly from the sales centers adjacent to the weavers’ workshops.
Buyers from all over the country visit these centers for affordable and authentic Jamdani.
Every Friday after Fajr, boats filled with passengers arrive at Demra Ghat in Dhaka, all heading to the century-old Jamdani market at Demra Bazaar.
While Jamdani markets are now held in different parts of Narayanganj, Demra’s market remains the oldest and most renowned.
Some of the sellers are also weavers themselves, bringing sarees they’ve worked on for weeks, months, or even a year.
Buyers purchase Jamdani both wholesale and retail, with many showroom representatives coming here to collect sarees for city outlets.
The market also attracts individual customers, especially women passionate about traditional sarees.
The quality is exceptional, and the prices are surprisingly reasonable. Nearly 4,000 weaver families supply sarees to this market.
Jamdani comes from weaving villages such as Rupganj, Tarabo, Noapara, Rupshi, Mogra Para, Sonargaon, Araihazar, and Siddhirganj—all converging into this vibrant hub of heritage and commerce.
Dhakai Jamdani Pricing and Varieties
Jamdani sarees are available at a range of prices, with affordable options starting from 500 to 1000 Bangladeshi Taka.
However, for high-quality sarees, the price can range anywhere from 5,000 Taka to as much as 5 lakh Taka. The market operates based on negotiations, not fixed rates, with prices fluctuating according to the design and quality.
Jamdani is crafted using four different types of yarn:
- Half Silk
- Full Silk
- Full Cotton
- Nylon (Although, nylon Jamdanis are rarely produced now).
The trading at the market starts early in the morning and continues until 9 AM, with buyers and sellers engaging in price negotiations throughout the day.
The price of a Jamdani saree primarily depends on the yarn count, which refers to the thickness of the yarn. The higher the yarn count, the finer and more delicate the fabric.
Weavers start with 40-count yarn and create sarees using 60, 80, 100, and even 120-count yarns. For special orders, customers can even request sarees made with 200-count yarn, which results in an exquisite and delicate fabric.
Conclusions
Due to the immense popularity of Jamdani sarees, there has been a diversification in the types of fabric used.
Apart from the traditional sarees, 1-piece, 2-piece, and 3-piece outfits as well as Punjabis are now crafted with Jamdani fabric.
There are numerous designs such as Jal Par, Jaba, Korola, Tera, Dubla, Jwala, Balihaar, Panna Hazaar, and Kotihaar, all contributing to the rich variety in Jamdani.
At the weekly market, thousands of sarees are sold. Buyers can get wholesale prices if they purchase four to eight sarees.
Every week, the market sees transactions worth nearly crore taka. This very market serves as a hub for the collection of sarees, which are then exported to Europe, America, the Middle East, and around the world.